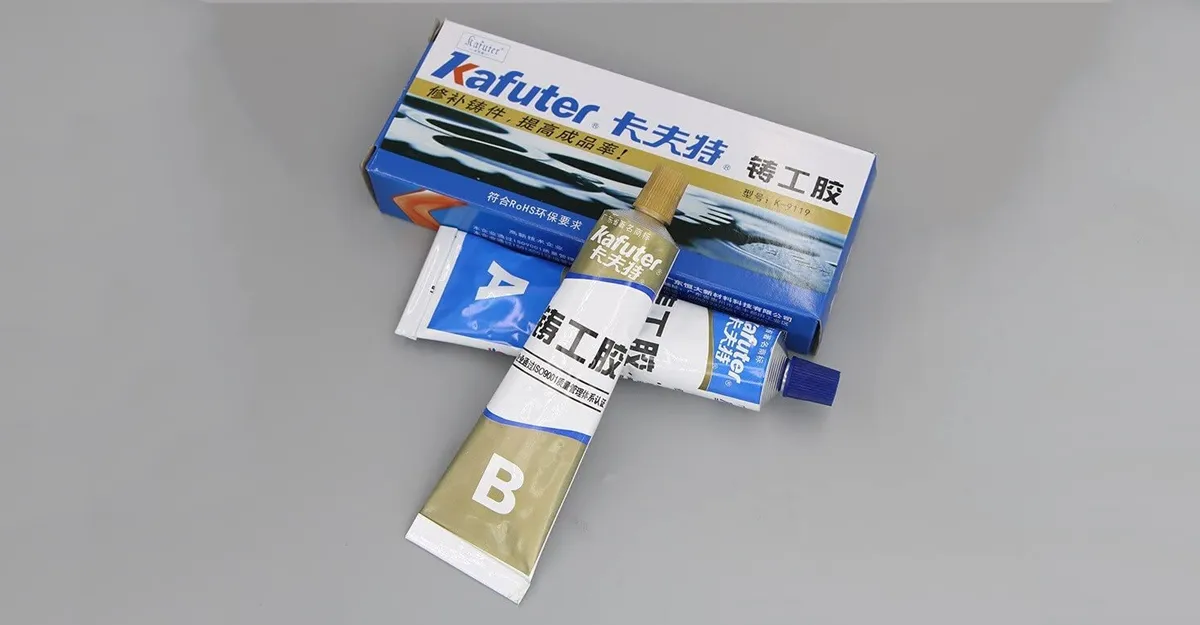
The Ultimate Guide to Metal Repair Paste and Cold Weld Solutions aims to provide you with all the necessary information to tackle metal repair projects efficiently. In the realm of metal repair, finding reliable and effective solutions is crucial. Whether you’re dealing with industrial machinery, automotive components, or household items, understanding how to utilize metal repair paste and cold weld methods can save significant time and resources. This guide covers the features, applications, and benefits of these repair materials, ensuring you can make informed decisions and achieve durable, long-lasting repairs. Get best Deal on Pidilite Multipurpose Home Kit Just ₹98
Introduction to Metal Repair Paste and Cold Weld
Metal repair paste is a specialized adhesive designed for fixing and bonding metal surfaces. It typically consists of a two-part epoxy system that, when mixed, creates a strong, durable bond capable of withstanding extreme conditions. This product’s key properties include high temperature resistance, excellent adhesion, and long-lasting durability, making it an indispensable tool for both industrial and household repairs. Metal repair paste can be used in a variety of applications, from heavy machinery to everyday household items, providing a reliable and efficient solution for metal repair needs. Understanding its composition and proper usage is essential for achieving optimal results and extending the lifespan of repaired items.
Pros
CONS
Our Verdict
4.2/5
Metal repair paste and cold weld solutions offer easy, durable, and versatile repair options for various metal surfaces, making them ideal for both professionals and DIY enthusiasts.
Understanding Cold Weld
Cold welding is a process where two metal surfaces are joined together without the need for heat. This method involves using a high-strength adhesive, like metal repair paste, to bond the metals at room temperature. Unlike traditional welding, cold welding does not melt the metals, making it a safer and more accessible option for non-professionals. The process relies on the adhesive properties of the metal repair paste to create a bond that is as strong as, if not stronger than, the original material. Cold welding is particularly useful in situations where heat could damage the components or where traditional welding equipment is not available.
Applications and Benefits of Metal Repair Paste
Metal repair paste is incredibly versatile and can be used in various applications. In industrial settings, it is ideal for repairing heavy machinery and equipment, providing strong bonds that can withstand high stress. In the automotive industry, it is commonly used to fix engine parts, exhaust systems, and other critical components. For household and DIY repairs, metal repair paste is perfect for mending metal furniture, appliances, and other items. The primary advantages of using metal repair paste include its quick and easy application, the elimination of the need for high temperatures, and the creation of strong and durable bonds that last, even under challenging conditions. These benefits make metal repair paste a preferred choice for both professional and amateur repairs.
How Cold Welding Enhances Metal Repair
Cold welding offers several advantages over traditional welding methods. It eliminates the risks associated with high-temperature welding, such as burns and fires, making it a safer option. Additionally, cold welding is cost-effective as it reduces the need for expensive welding equipment and materials. This method is accessible to non-professionals, allowing anyone with basic DIY skills to perform effective metal repairs. Cold welding is particularly useful in situations where high heat could cause damage or warping to delicate components. Numerous case studies and success stories from various industries highlight the effectiveness of cold welding, showcasing its capability to produce durable, high-quality repairs without the complexities of traditional welding.
Step-by-Step Guide to Using Metal Repair Paste and Cold Weld
Using metal repair paste and cold weld solutions effectively requires careful preparation and application. Here’s a detailed step-by-step guide:
Preparation
Begin by thoroughly cleaning the metal surface to remove any dirt, grease, or rust. Use a degreaser and a wire brush or sandpaper to ensure a clean and slightly roughened surface, which enhances adhesion. Gather all necessary tools and materials, including the metal repair paste, mixing sticks, and clamps.
Application Process
Mix the two-part epoxy according to the manufacturer’s instructions. Typically, you’ll combine equal parts of the resin and hardener until the mixture is uniform. Apply the paste to the prepared surface, ensuring an even layer that covers the repair area completely. Use a putty knife or similar tool to smooth the adhesive.
Curing Time and Conditions
Allow the repair paste to cure under recommended conditions. Most products require a curing time of 24 to 48 hours at room temperature. Avoid moving or stressing the repaired area during this period to ensure a strong bond.
Post-Application Tips
To ensure maximum bond strength, inspect the repair after curing and perform any necessary touch-ups. Regularly check the repaired area to maintain its integrity, especially in high-stress applications. Proper maintenance will extend the lifespan of the repair.
Expert Tips and Troubleshooting
- Optimal Conditions for Use
- Apply metal repair paste in a well-ventilated area at temperatures between 50°F and 90°F (10°C and 32°C).
- Ensure low humidity levels to prevent moisture from affecting the curing process.
- Surface Preparation
- Thoroughly clean the surface to remove dirt, grease, and rust.
- Lightly sand the area to create a rough texture for better adhesion.
- Mixing Ratios
- Follow the manufacturer’s instructions precisely for mixing the two-part epoxy.
- Use a clean, disposable container and mixing stick to avoid contamination.
- Application Techniques
- Apply the paste evenly and press it firmly into any cracks or gaps.
- Use a putty knife or similar tool to smooth the surface for a seamless finish.
- Curing Time
- Allow the adhesive to cure undisturbed for at least 24 hours.
- Avoid moving or stressing the repaired area during the curing process.
- Troubleshooting Common Issues
- If the adhesive fails to cure completely, ensure proper mixing and environmental conditions were met.
- For bond failures, re-clean the surface and reapply the adhesive, ensuring all steps are followed accurately.
- Post-Application Care
- Regularly inspect the repair to ensure its integrity.
- If needed, sand and paint the cured adhesive to match the surrounding surface.
Real-World Applications and Testimonials
Real-world applications of metal repair paste and cold welding solutions demonstrate their effectiveness and versatility. In industrial settings, detailed examples show how these products have extended the life of machinery and equipment, saving time and money on replacements. DIY enthusiasts and homeowners also provide positive feedback and practical tips, sharing their success stories of using metal repair paste for various home projects. These testimonials highlight the product’s reliability and ease of use, making it a valuable tool for a wide range of repair needs. The experiences of both professionals and amateurs underscore the importance of having a dependable metal repair solution.
Conclusion
Metal repair paste and cold weld solutions are indispensable tools for anyone dealing with metal repairs. By understanding their properties, applications, and benefits, you can make the most of these materials, ensuring effective and long-lasting repairs. Whether you are a professional or a DIY enthusiast, these products offer reliable and efficient solutions for a variety of metal repair challenges. With proper usage and adherence to the guidelines provided in this guide, you can achieve high-quality repairs that extend the life of your metal items.
Leave a Reply